个人观点,仅供参考
说明:APS高级计划和排程作为MOM核心软件模块,是介于ERP与MES之间。从2017年开始随着智能制造的热度上升而走热,也引起了国内众多大咖的热议:反对者有之,实践者更多。
个人认为,随着多品种、小批量、短交期、定制化的兴起(趋势非常明显,而且是现实了),要增加有效产出,必然需要集批:在满足交期和产出的情况下,合理集批。因为非工作时间=换型次数*换型时间。换型时间一般由精益生产中的SMED(快速换模)解决,但是次数的优化必然需要用APS来解决了。
当然,APS不仅仅是这些功能,个人结合中小企业的具体实际,定义了APS的关键功能:
1、负荷展望(AP部分)
APS可以基于预测订单,并结合现有已经确定的订单,进行产能和物料的展望,经从当前时刻至未来所有预测订单+正式订单的负荷和物料的展望,判断出负荷的紧张状态和订单完工预计、产能约束和物料约束的状况。
2、MRP计算
APS是基于物料约束、产能约束、工艺约束三个状态(工厂建模)下、工单下达规则(全局前置JIT、资源前置JIT、鼓缓冲绳)、优化规则(交期优化、产出优化、财务指标优化)情况的计划和排程。
MRP也是APS的基本功能,依据前置周期和BOM计算物料可得。
3、异常和KPI模拟
APS可以非常方便地模拟工厂营运过程中的异常情况:
第一,交期异常模拟
提前和延后订单、插入订单时,对其余订单交付的影响,可以得出影响程度。可以进行变更前后的报表,供计划人员评审。
第二,产能异常模拟
可以模拟设备(资源)临时异常,对订单交付的影响。可以将设备(资源)的临时停机(日期、时段和周期),在What-if场景中进行模拟,供计划人员评审。
第三,供应商异常模拟
供应商来料异常一般分为到料日、到料数量两个维度。APS系统可以针对这两个维度进行统一的异常。
第四,KPI指标模拟
因为APS是可以优化的系统,尤其是排程部分的优化,对工厂运营的KPI指标的影响比较大,不仅影响客户服务水平(准交率、交货周期等),尤其影响工厂的产出(有效产出、生产成本等)。
APS可以在What-if场景里,通过调整优化规则(交付、产出和财务指标),与实例进行对比,以选择更加好的优化规则,实现持续改善。
4、优化排程
APS可以依据录入的销售订单(生产任务)并选择预计、计划等状态,实现优化排程:给出工序工单的计划开始时间(EPST)和计划完工时间,实现以下同步:
第一,计划和排程的同步
计划和排程是不同对象、目标和时间维度的作业。往往计划考虑交付、排程考虑产出。APS将计划和排程过程同步化,并优化。
第二,全厂范围内工序工单的同步
通常情况下,手工进行计划和排程时,PMC考虑计划:车间级工单的投放。车间的调度员考虑的是工序工单的投放,考虑产出。而且,不同车间的计划员不同,不同车间的调度员更是不同。
计划与计划之间、计划与调度之间、调度与调度之间一般均通过调度会和线下交流的方式实现。存在考虑维度窄、时间短、协同困难等问题
第三,交付和产出的同步。而APS是主计划员利用系统统一计划和排程,而且直接计划和排程的维度覆盖到全工厂、工序级、单个设备级的颗粒度上,确保实现整体的最优化。
所以,用好APS协同工具,可以大大提高计划的作业效率,提高计划作业精度,实现工厂的整体优化。
当然,APS的应用需要一定的前置条件:
其一,最好有ERP、MES的系统基础
其二,BOM、工艺路线、排程规则、约束条件、缓冲周期等基本参数比较完善。
其三,基础管理水平相对比较好:完善的组织结构和编制,合理的管理流程和制度等等。最重要的是,需要有足够的预算和心态来做APS。离开管理基础、基础数据、基本预算的APS还是不靠谱的。希望大家切记。
声明:本文章仅仅代表个人观点,仅供参考。

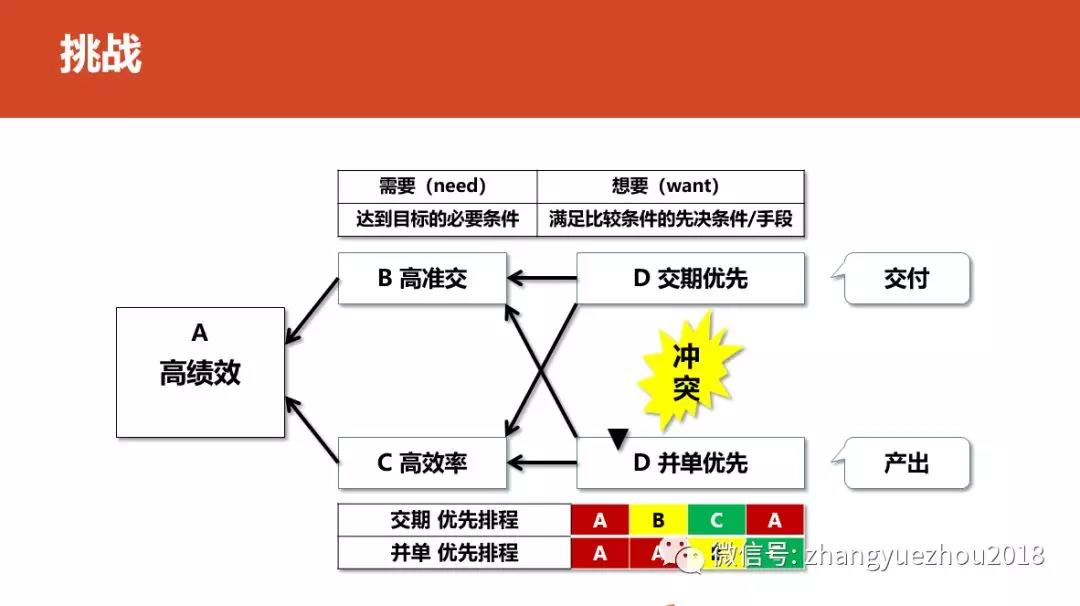
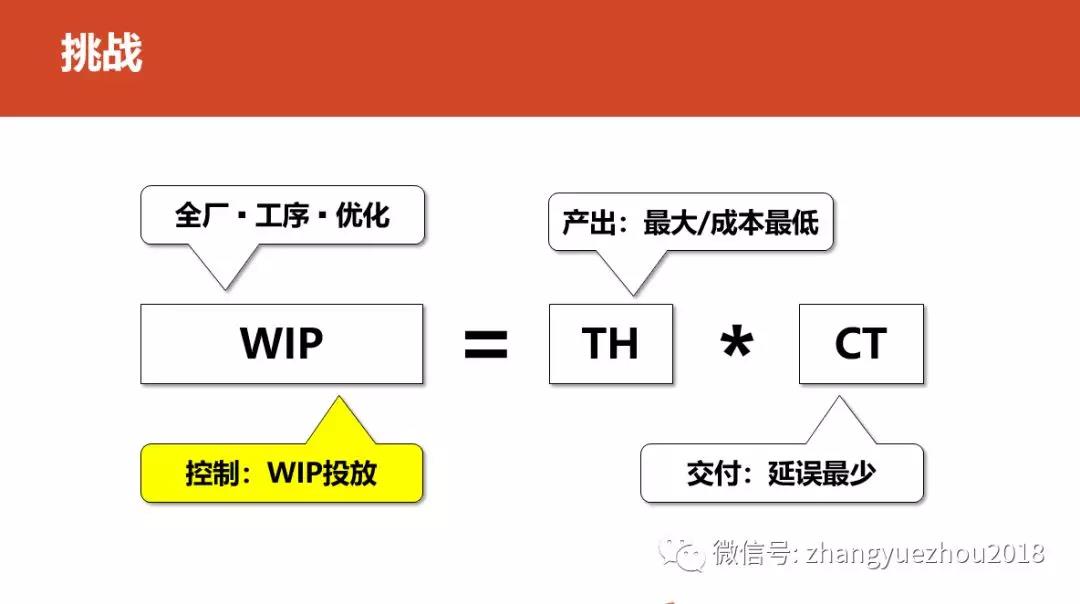
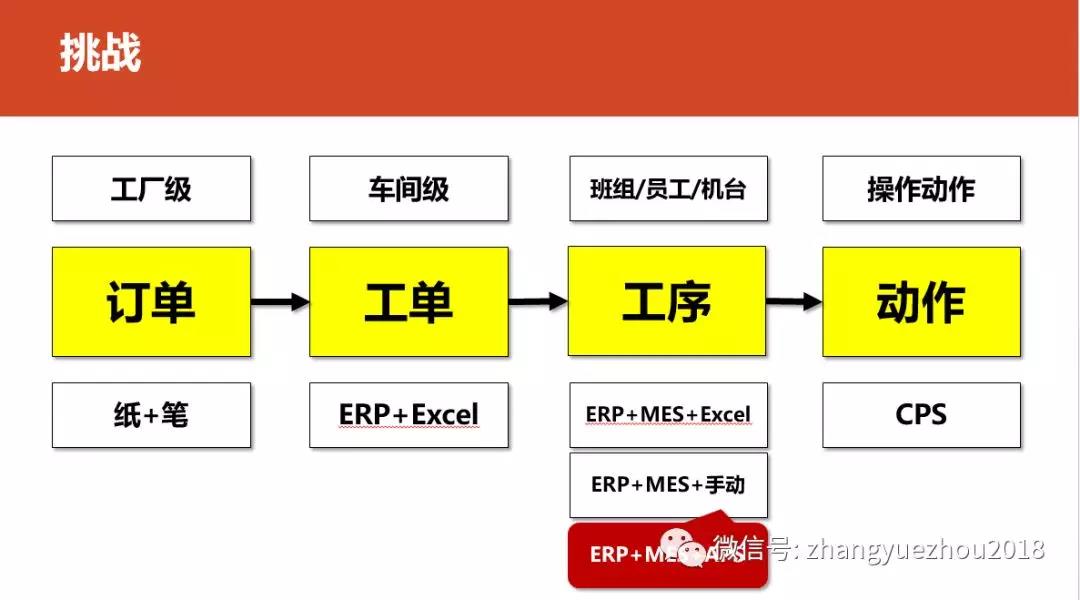
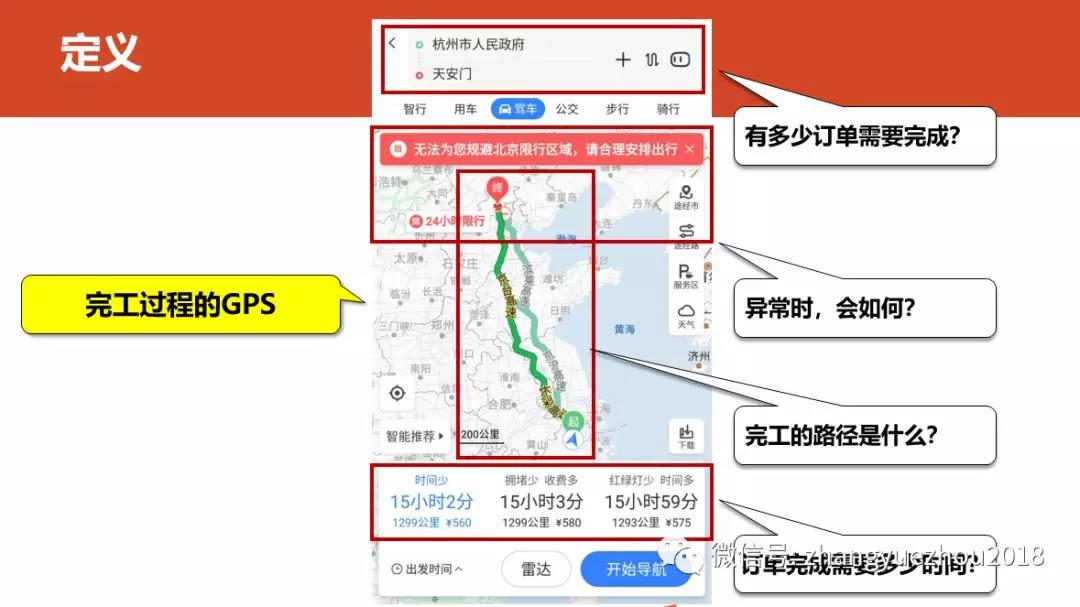
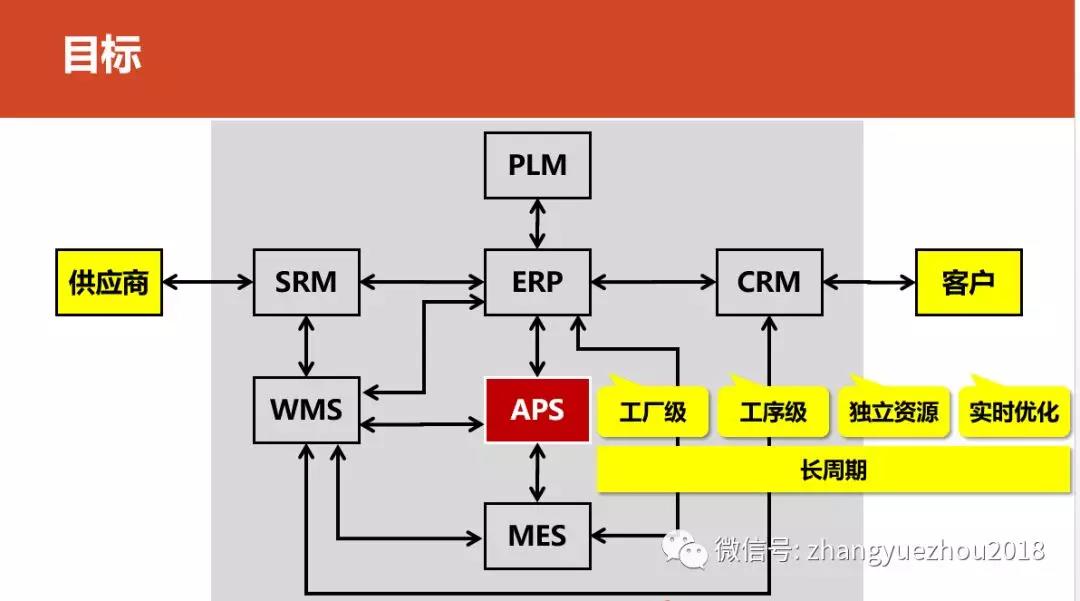
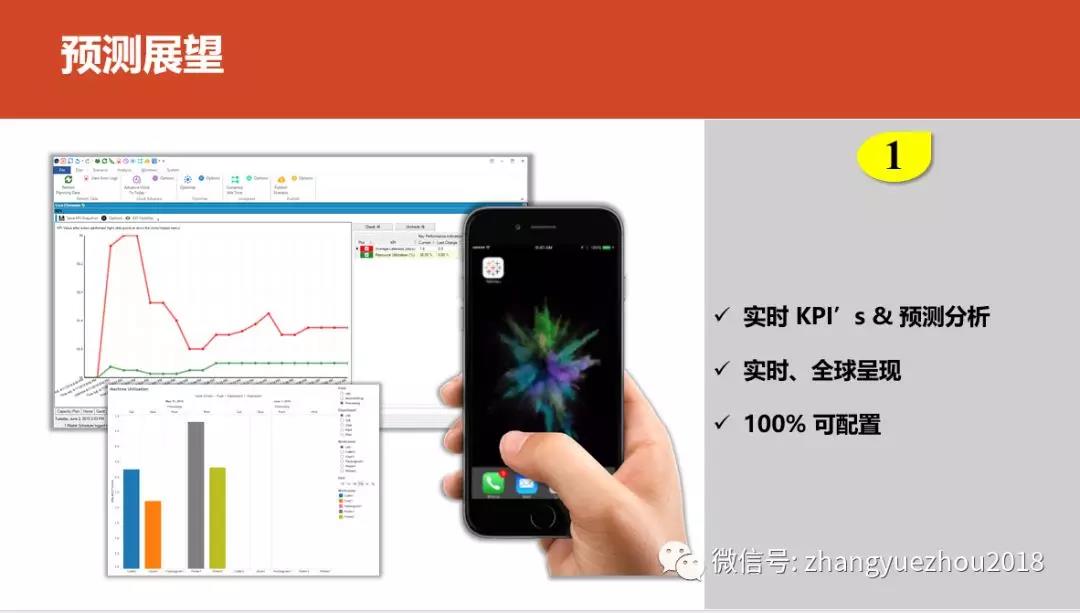
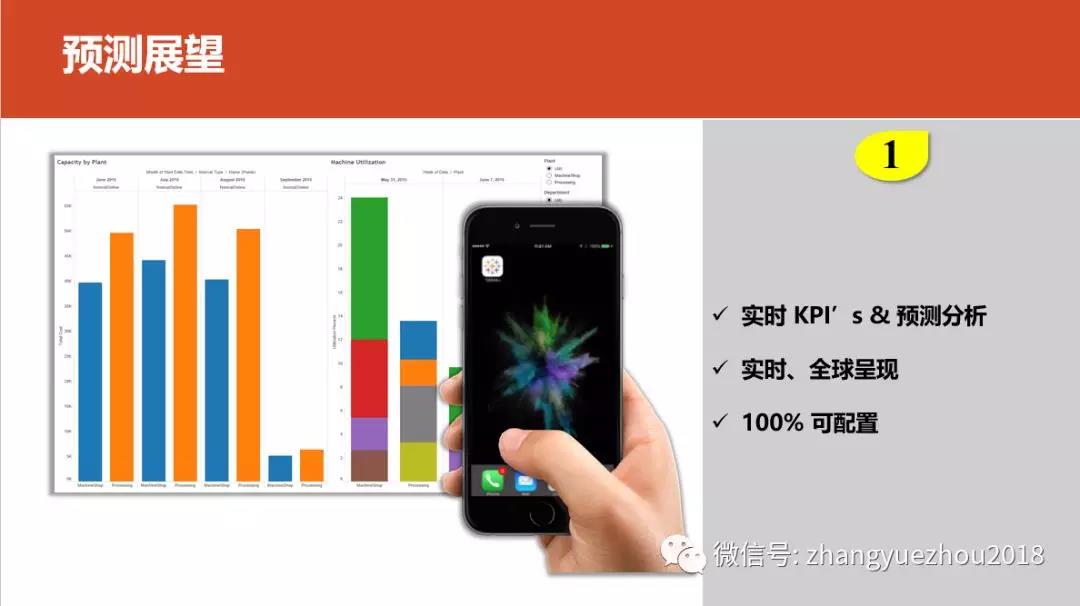
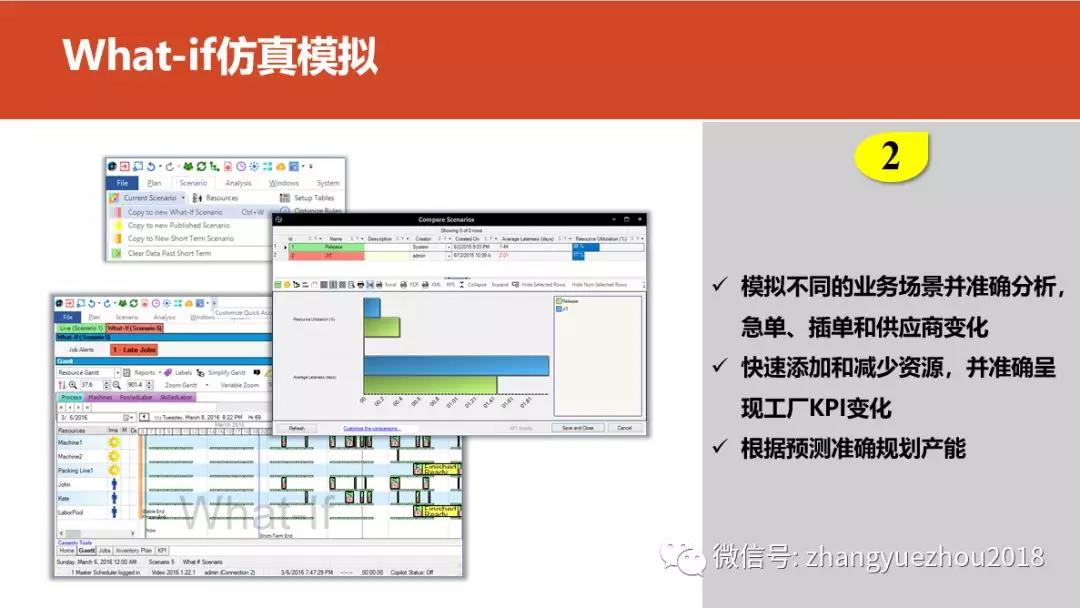
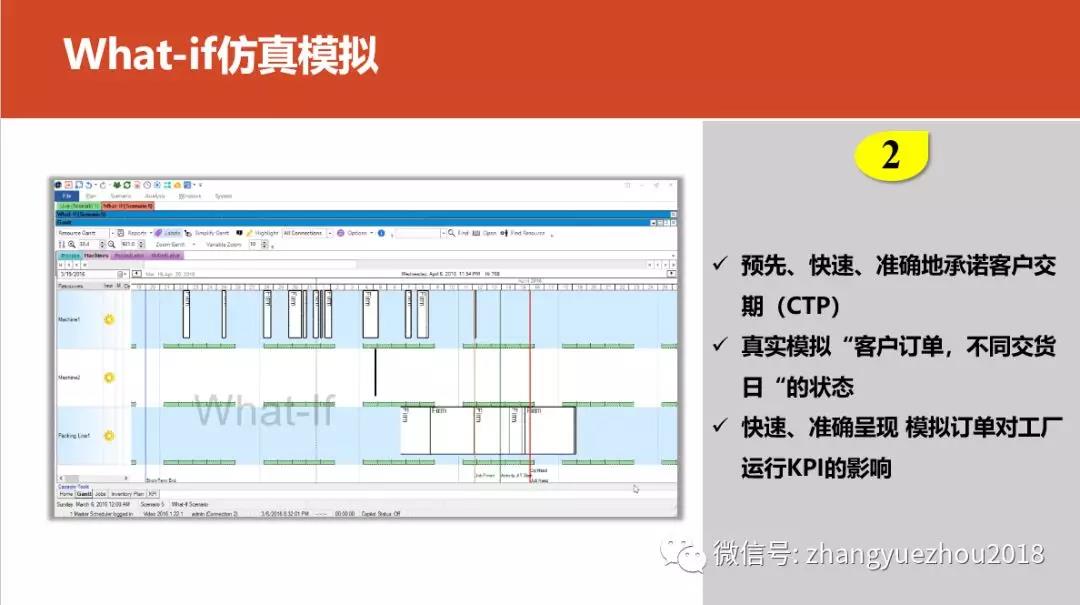
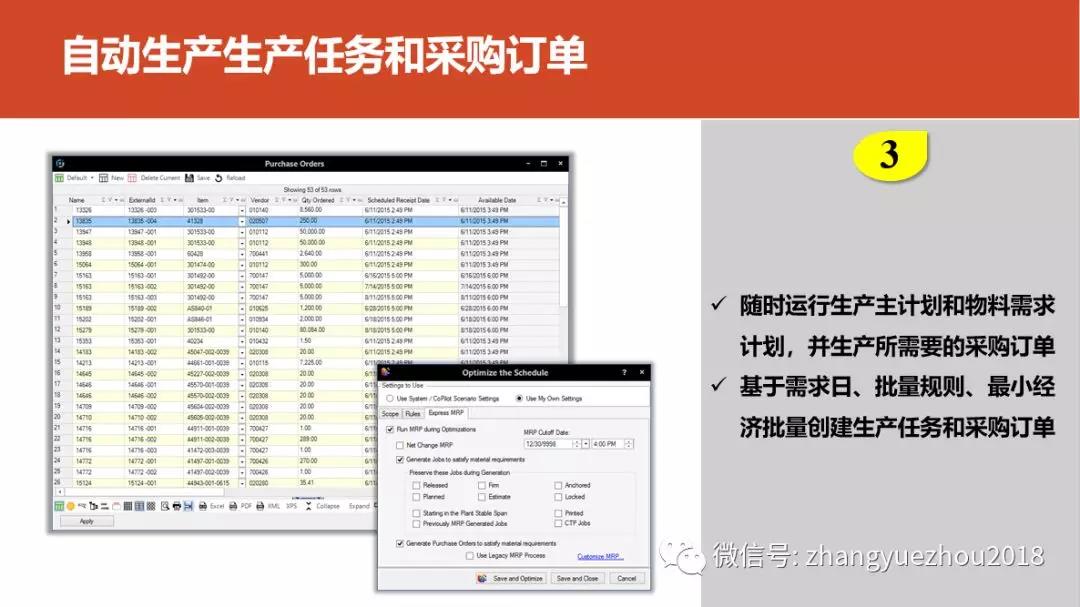

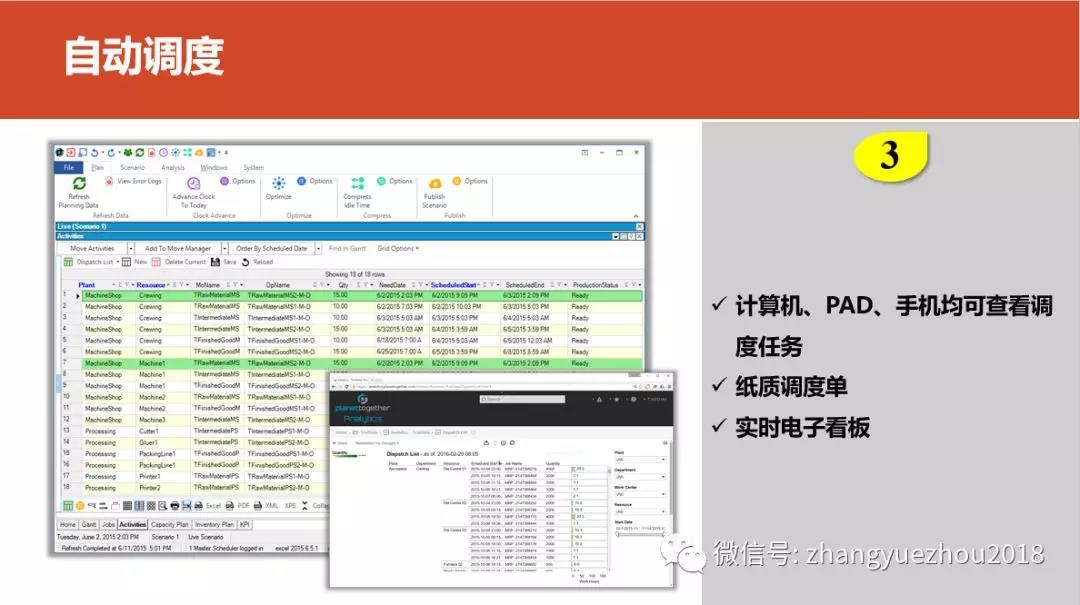
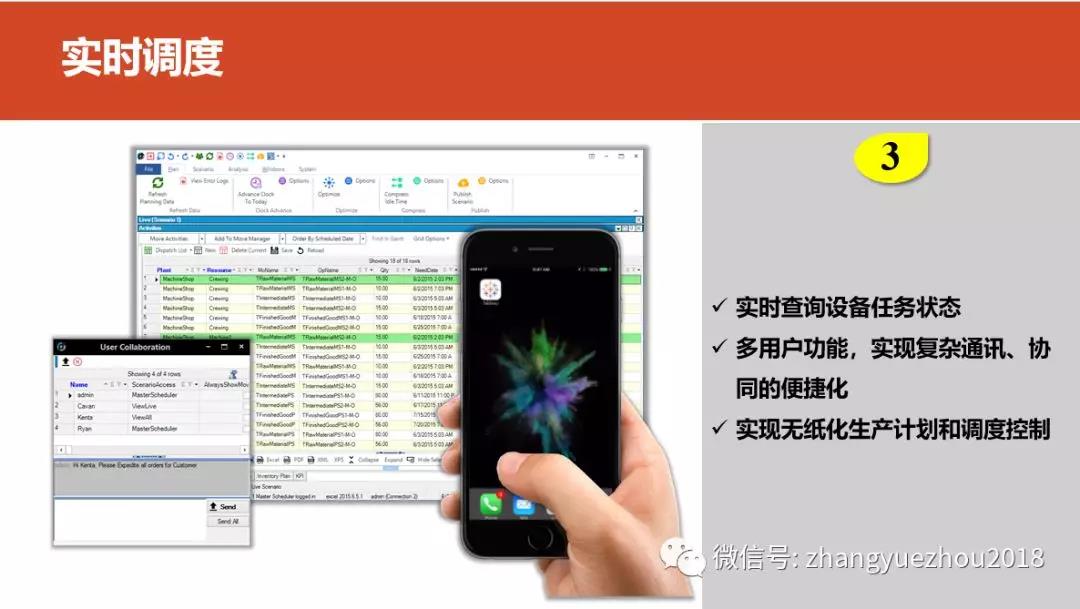

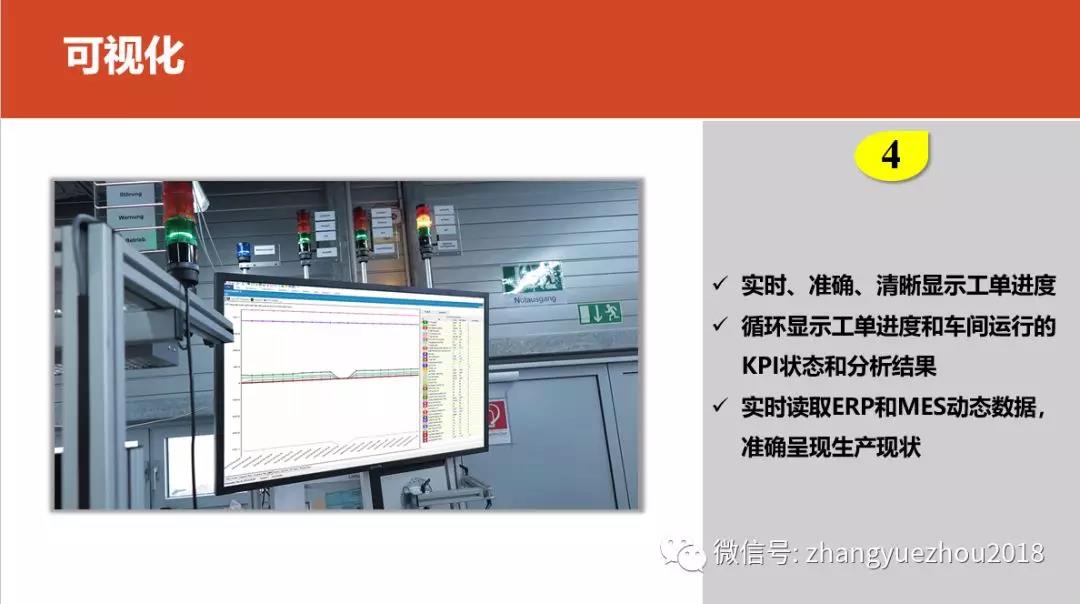


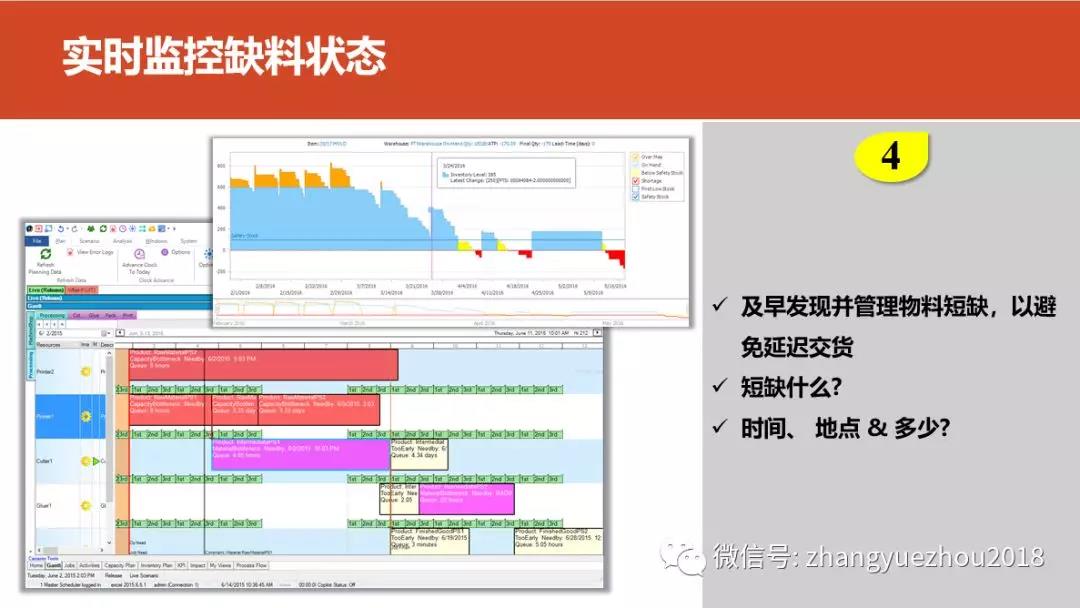
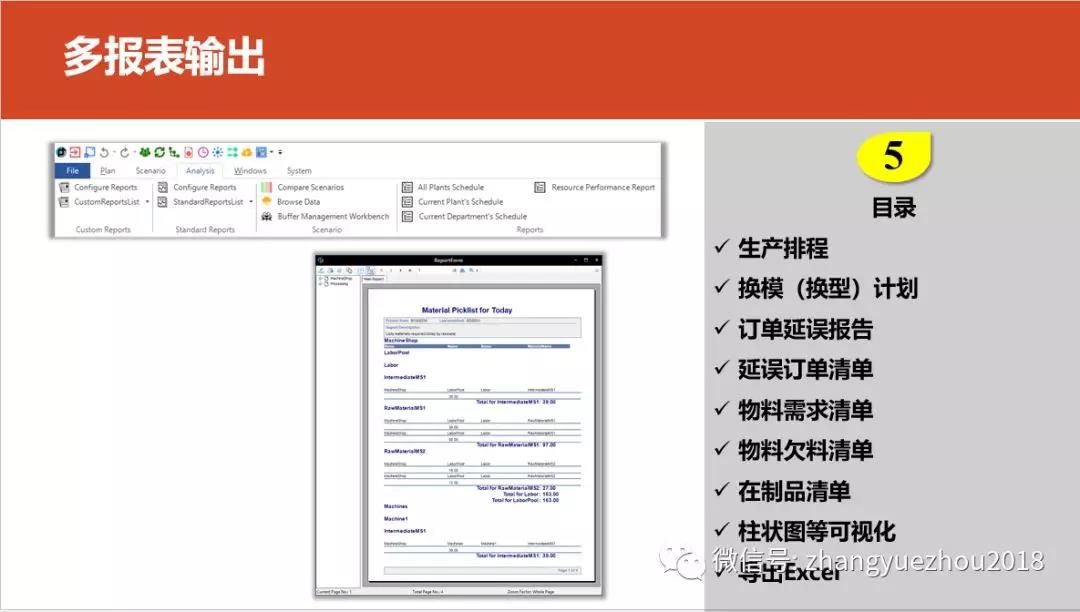
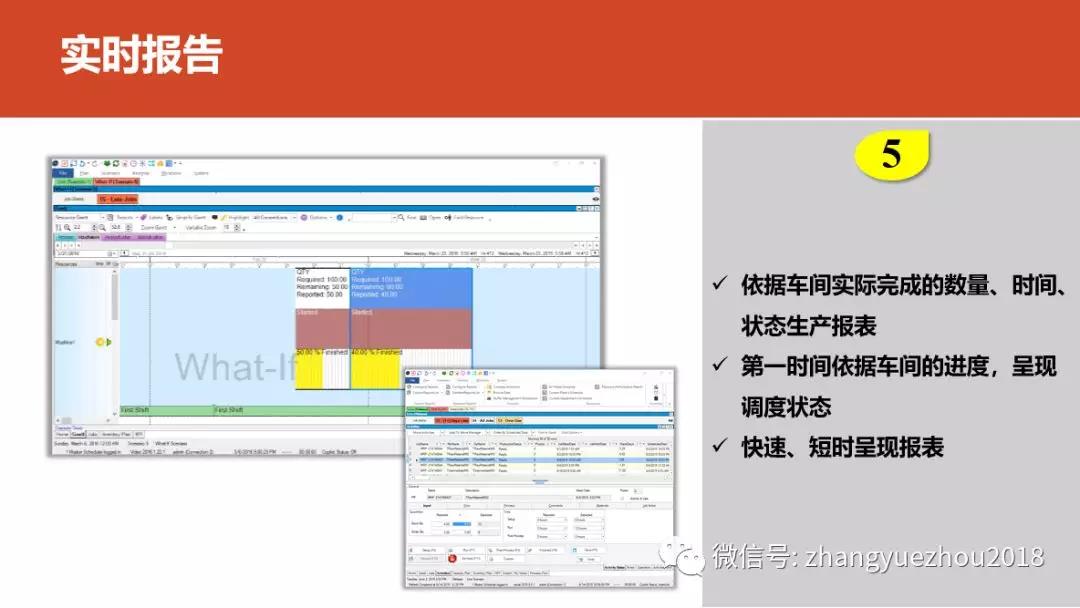